saved by using Prism
cable-stayed bridge in the world
of concrete poured
long modules installed
The Queensferry Crossing – the longest three-tower, cable-stayed bridge in the world – forms the centrepiece of the Scottish Government’s unprecedented £1.35bn upgrade to the cross-Forth transport corridor in the east of Scotland. Officially opened by Her Majesty The Queen in September 2017, this new iconic structure has been designed to complement the existing road and rail crossings and safeguard a vital connection in the country’s transport network.
Working for client Transport Scotland, the project has been led by the Forth Crossing Bridge Constructors (FCBC) consortium, consisting of HOCHTIEF Solutions AG, American Bridge International, Dragados S.A. and Morrison Construction.
During this two-year project, SES Engineering Services’ (SES) role was to deliver Mechanical, Electrical and Plumbing (MEP) services to the new replacement road bridge’s North and South approach viaducts, the cable-stayed bridge itself, its three towers and abutment buildings.
Offsite working on this project was not just a consideration, it was a necessity. With each 800-tonne deck section completed onshore then manoeuvred by boat from the port into place under the bridge, the use of offsite methods impacted every stage of SES’ project.
SES’ main delivery strategy on this project was to maximise the amount of M&E services that could be installed within the individual CSB deck sections whilst remaining onshore. In order to achieve this goal, SES established its UK-first, project-specific offsite prefabrication facility in Rosyth away from Prism’s Yorkshire base to manufacture the containment and pipework service modules.
As the first MEP services contractor to achieve BRE Accredited BIM Level 2 Certification, SES and Prism provided true digital manufacturing functionality by marrying digital processes to limit waste, with the ability to create lean modules easily installed by engineers’ offsite in Scotland.
This overwhelming commitment to offsite engineering dramatically reduced the need for working at height and saved more than 32,500 hours of labour, making the comparison to out-dated on-site methods almost immeasurable. Initially manned by a team of Prism staff, over time the factory was handed over to an SES team of locally upskilled labour breaking new ground for cost and time efficiency savings.
Steve Joyce, Business Director North and Scotland, SES commented:
“The crossing represents leading-edge, 21st Century civil engineering. It’s a rare opportunity to be involved in building a new major infrastructure project of international significance. We knew this was the perfect opportunity for us to showcase the true capabilities of offsite technologies; and as part of a truly collaborative approach, this is a once-in-a-lifetime project designed with M&E at its core.”
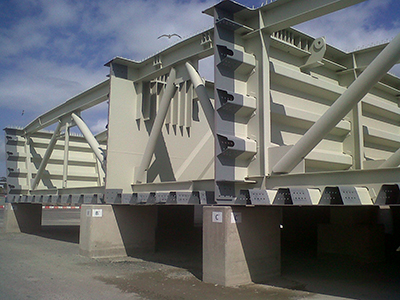
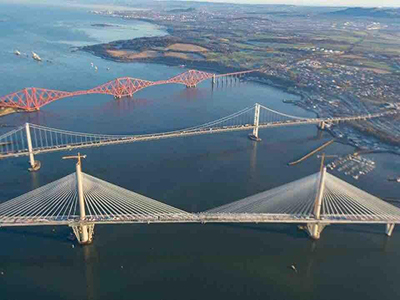
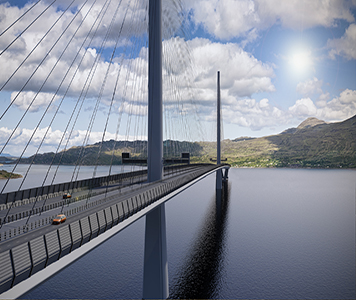
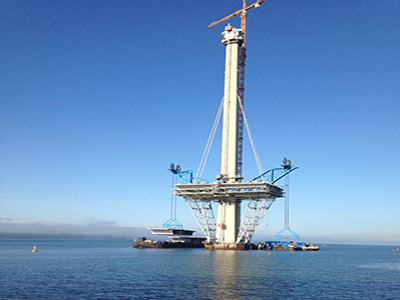
Other Case Studies
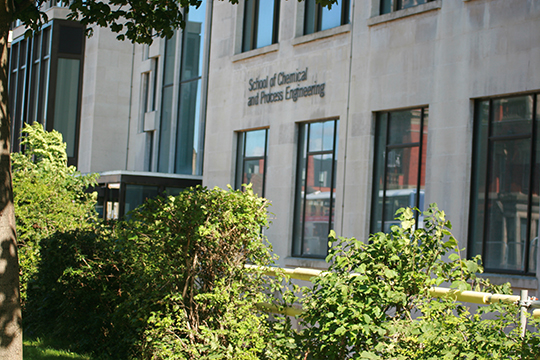
University of Leeds – School of Chemical and Process Engineering
The University of Leeds embarked on an ambitious £520m five year programme of works to transform its entire campus to support its vision for increasing knowledge and opportunity with a focus on world-leading research, collaborative industry partnerships and further enhancing the student experience for 1,000+ students who come from 70+ countries to study in the building.
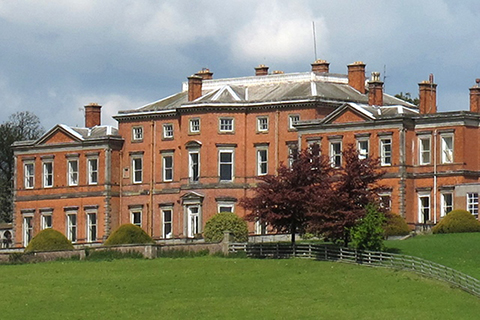
The Defence and National Rehabilitation Centre (DNRC)
Handed over by Prince William, the Duke of Cambridge and Prime Minister, Theresa May in June 2018, the DNRC will be operated by the Ministry of Defence when it opens later this year.
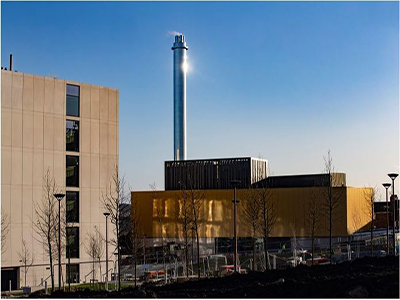
Newcastle District Energy Centre
Supporting the city of Newcastle Upon Tyne in its endeavours to go carbon neutral by 2030, SES Engineering Services (SES) was directly appointed by Engie as main contractor to design and install complex MEP solutions on Newcastle District Energy Centre.