service cupboards installed
saved by using Prism
listed gasholders
and tested pipework
Set in King’s Cross – one of the largest areas of central London to be developed in the last 150 years – the circular Gasholders London project is a pioneering example of cutting-edge offsite manufacturing and prefabrication. Housing 145 luxury apartments, the project is the sixth M&E design and build project for SES Engineering Services (SES) on the iconic central London redevelopment.
The Gasholders scheme comprises three circular luxury residential buildings sat within original Grade II-listed, cast-iron gasholder guide frames, twelve, nine and eight storeys high which features 145 distinctive canal-side apartments and penthouses. They stand at the heart of the King’s Cross development, the largest piece of central London to be developed under a single ownership in the past 150 years, which is set to create 2,000 new homes, 20 new streets and 10 new public squares.
Working in close collaboration with developer King’s Cross Central Limited Partnership, SES’ design and installation teams as well as its specialist offsite prefabrication facility, Prism, delivered a pioneering solution for this one-of-a-kind project saving over £500k on the overall project cost.
Unfazed by the technical challenge of delivering tailored M&E services for three circular buildings, SES delivered a complex circular module solution. The main service risers covered six riser shafts each extending up the three gasholders incorporating 1.7km of finished and tested pipework, ductwork and electrical containment.
All modules were manufactured and tested in factory conditions at Prism, ensuring that the modules were constructed to the highest standard and reducing the programme risk.
The project was set with high offsite manufacturing targets; in addition to the circular modules, SES delivered the BIM and modelling for M7E service risers in each gasholder, as well as full take-offs and cut lists for the basement plant areas and corridors.
SES also delivered 270 apartment service cupboards. A first of its kind, these pioneering installations contain a fully integrated ‘plug and play’ M&E services hub for each apartment. Each included a heat interface unit, MVHR units, underfloor heating manifolds, consumer unit, BT Home Hub and space for a washing machine.
Combined with a substantial reduction in logistical cost and time, these decisions enabled SES to deliver a build time of approximately 10,000 hours, 29,000 less than what would be anticipated with traditional onsite methods.
David Jenkins, Business Director London and South East, SES commented:
“The nationwide recognition of our award -winning offsite solutions on previous King’s Cross projects, such as the nearby Plimsoll Building, has been a fantastic stepping stone towards the unique and fascinating challenge we faced with the Gasholders London project.
“On a project like this, the devil is in the detail and our Prism facility is at the forefront of M&E installations. Our ability to deliver innovations such as circular modules and our prefabricated service cupboards, on logistically challenging city-centre projects such as this, are crucial to our ongoing and successful growth strategy in London and the South East.”
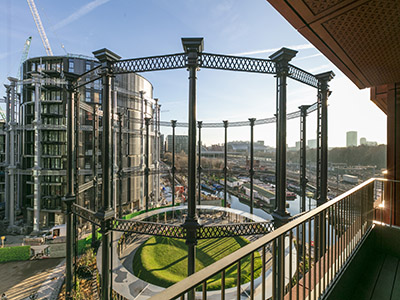
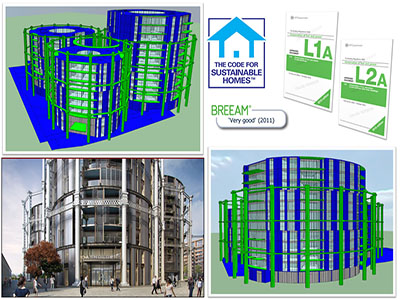
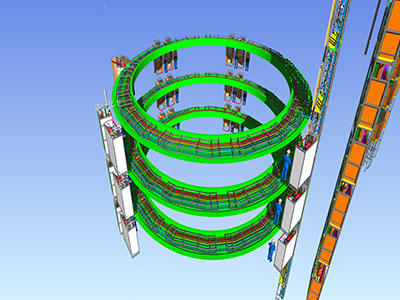
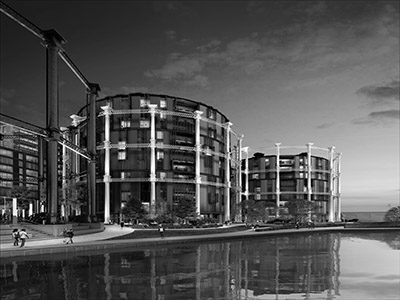
Other Case Studies
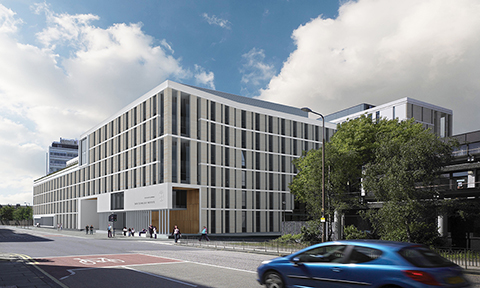
The University of Edinburgh - Data Technology Institute
Securing the contract for Edinburgh University’s Data Technology Institute represented a major milestone for SES operations in Scotland.
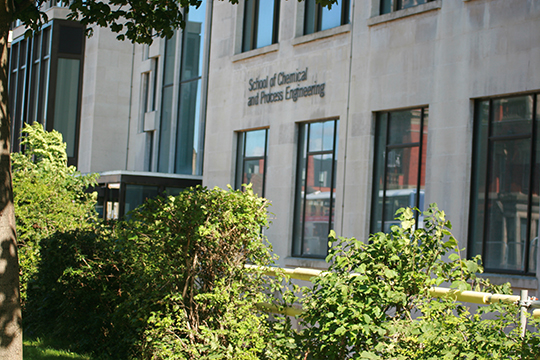
University of Leeds – School of Chemical and Process Engineering
The University of Leeds embarked on an ambitious £520m five year programme of works to transform its entire campus to support its vision for increasing knowledge and opportunity with a focus on world-leading research, collaborative industry partnerships and further enhancing the student experience for 1,000+ students who come from 70+ countries to study in the building.
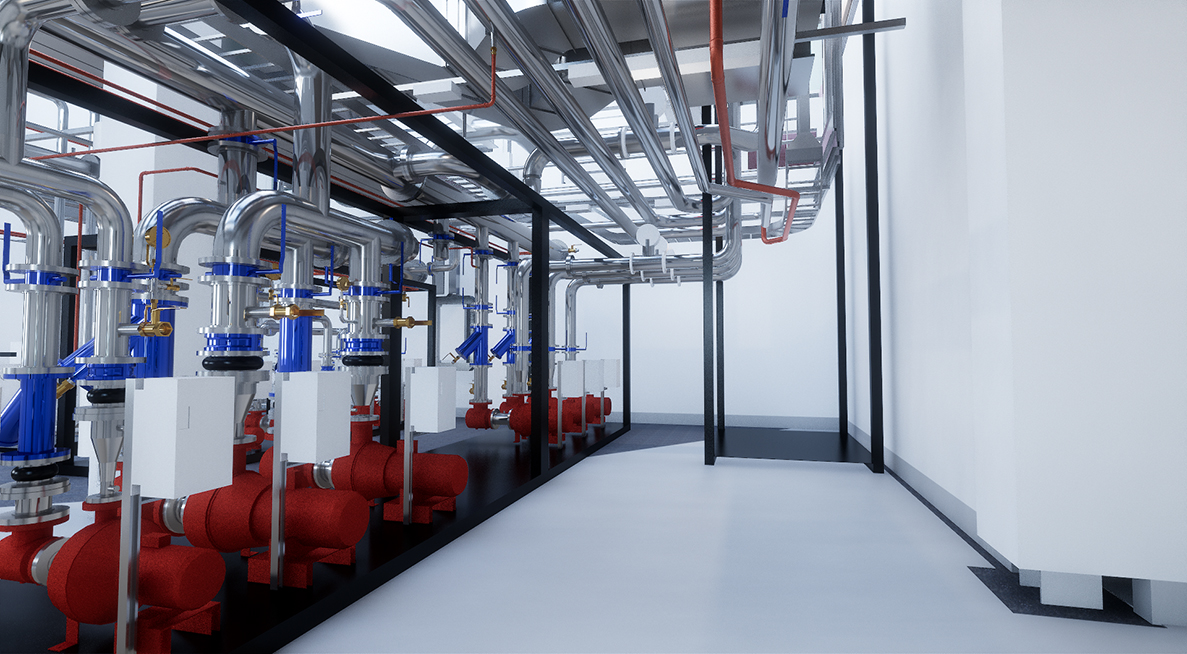
GSK Aseptic Manufacturing Facility - Q Block
SES worked to a detailed schedule of works to install all mechanical and electrical (M&E) building services, ensuring that there was minimum disruption to the live manufacturing site which completed in January 2020.